Warehouse Management Systems & Inventory Management Systems: What’s the Difference?
If you keep inventory in a warehouse, you might wonder why there are inventory management systems and warehouse management systems (aka WMS inventory). The only thing you keep in the warehouse is inventory, so if you’re managing one, then you’re managing the other, no?
No. But you’re not the only one who’s confused by the two. And they aren’t really that far apart anyway.
In a nutshell, the basic difference between a warehouse management system (WMS) and an inventory management system (IMS) is that one involves tracking counts of individual products or SKUs and the other involves tracking units of space, including compartments and bins.
If you had your own warehouse, and you stored fairly large products, let’s say something big enough to fill an entire bin or compartment, you might not need an inventory system because it would be relatively easy to keep inventory using the WMS and count stock by hand.
Conversely, if you had a number of smaller products, let’s say packs of gum, and you knew exactly how much space certain quantities of gum used up, then you might be able to get away with only and IMS, because you could manage your space through your inventory counts.
But, after all that, in both those scenarios, there would still be things you couldn’t do without using both systems. Yes, you might be able to get away with a physical count of your large warehoused products, but an IMS completely eliminates the need to do physical counts, at least until it’s inventory audit time. In the gum scenario, you could be wasting more warehouse space than you think, even though you’re managing the gum space relatively well.
The Real Differences (and Similarities) Between Inventory and Warehouse Management Systems
Aside from precisely what they are used to track, the major difference between an IMS and a WMS is complexity. In addition to managing warehouse space, a WMS does extra duty due to the other functions of a warehouse, from issuing order receipts to shipping manifests.
A WMS will also track every bin and compartment so you can manage multiple bins of the same product and distribute them to different parts of the warehouse to optimize space utilization. It will also tell you where those bins are at any given time, whereas an IMS will only give you a count of each bin.
The complexity of both systems adds so much versatility to your warehouse operations versus operating without them. Using more of your expensive warehouse space and keeping inventory at just-in-time levels are just two of the major benefits that an IMS and WMS deliver.
Other tasks that make a WMS a larger part of the overall logistics of a warehouse, include production supply, sales and distribution, and quality management.
But as we said, an IMS and a WMS are also not very far apart in the roles they play in the warehouse. So they play almost the same roles for certain functions.
Both systems actually monitor product levels. They track parts and products using barcodes. They both play similar roles in other warehouse functions like cycle counts, order picking and packing, and shipping and receiving.
If you use a third-party logistics company for all or part of your warehousing requirements, it pays to work with one who uses the most up-to-date IMS and WMS systems. When you do, it can feel like you are in complete control of your own warehouse because of the detailed information the systems can put at your fingertips.
Stay Up-To-Date
There's always something new from PiVAL
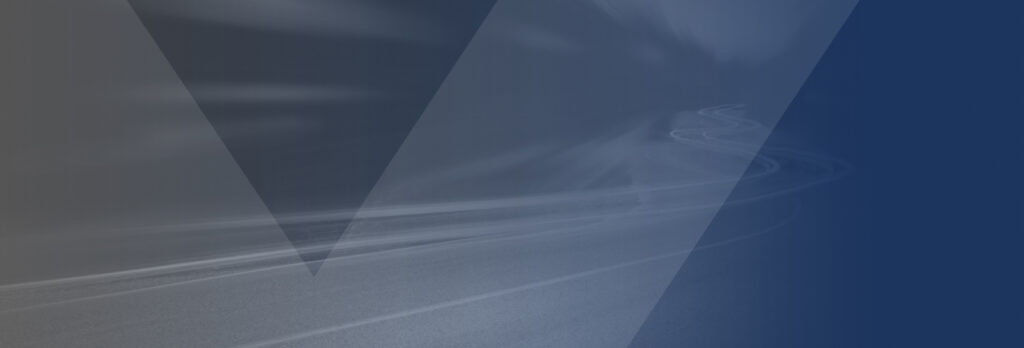
Comments are closed.